- June 16, 2020
- Posted by: simba001
- Categories: Benefits of POS, Reatil POS Insights
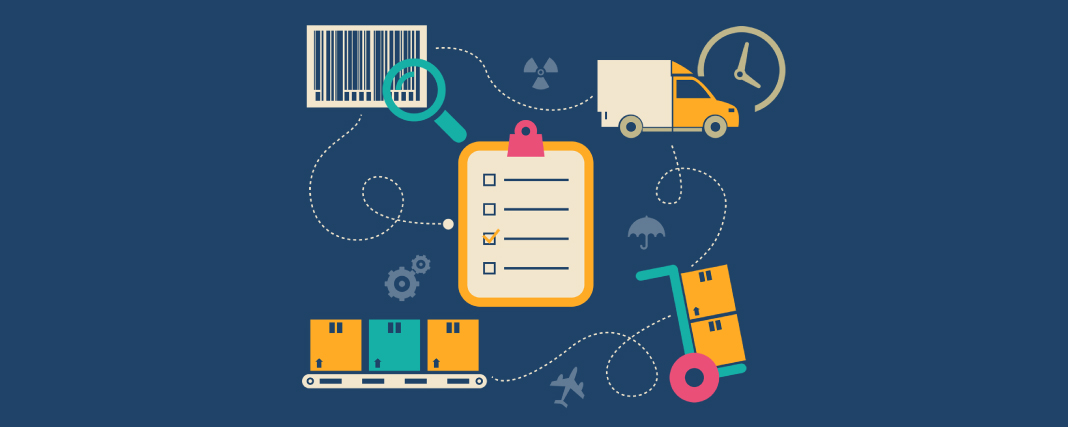
When’s the last time you did inventory reconciliation – comparing the inventory records from your point of sale system to the counted inventory levels in your store?
If you’ve ever performed a physical inventory count, you know that inventory records and the results of an inventory count rarely match and, when that happens, you need to reconcile inventory records against the physical inventory in stock.
In this post, you’ll learn exactly what inventory reconciliation is, how it works, why it’s important and how to reconcile inventory records without having to close up shop and miss out on sales opportunities.
When’s the last time you compared the inventory records from your point of sale system to the counted inventory levels in your store?
What is inventory reconciliation
Inventory reconciliation is the process of matching inventory levels in your POS system with the physical inventory levels in your store and stockroom. By reconciling inventory, merchants can address discrepancies between the results of their physical inventory counts and the recorded inventory levels in their point of sale.
By reconciling inventory often, retailers can better understand why there are discrepancies and better prevent them in the future.
Why is inventory reconciliation important?
If inventory records don’t match records of inventory on hand, merchants have a problem.
Even with the right inventory management software, shrinkage (either an excess or shortage of inventory on hand compared to recorded inventory levels that cannot be accounted for) is inevitable.
By cycle counting and reconciling inventory frequently, merchants can better monitor shrinkage and uncover the reasons behind discrepancies. While it may be caused by administrative human error—like inaccurate inventory counts or misplacing items in the stock room—it may also be caused by a larger issue like employee theft or supplier fraud.
If your shrinkage rate grows from one inventory reconciliation to the next, it may be a signal that you need to perform some investigative work and establish some loss prevention strategies to keep that number as low as possible.
Human error is one of the primary causes of stock discrepancies, but when equipped with the right tech, merchants can improve the speed and accuracy of their inventory counts.
How inventory reconciliation works
While the process of reconciling inventory may vary from one merchant to another, there are steps that each typically follows to varying degrees:
Perform a physical inventory count
A physical inventory count is when a retailer counts all of their store and stockroom. Typically, inventory counts are performed by an assigned team of workers who will count the inventory levels of each item and record the results either with a pen and paper or using an Excel spreadsheet .
While some merchants opt to close their store during typical business hours to perform a full inventory count, others opt to pay employees overtime to count inventory after business hours. While this method may require that a merchant pay its counters overtime, it also enables them to transact with customers throughout the day.
Compare count results to inventory records
Next, employees need to compare the results of their inventory count to the inventory levels recorded in the point of sale system.
While comparing recorded inventory levels to the results of their count, employees may uncover discrepancies—that is, when recorded inventory levels and the results of a count don’t match. Discrepancies can occur because of a host of reasons: from administrative stock-keeping issues to bad math, human error, theft or fraud.
Address missing items
Once you pinpoint any discrepancies, the next step is to address them and find out why they’re occurring. This involves digging through previous transactions and receipts to identify whether or not certain item sales have been overlooked.
Pinpoint the source of discrepancies
When the source of discrepancies can’t be addressed by verifying past transactions, it may be time to look into other possible causes like theft. You may never know who is committing the theft, but by securing your store and stock room with surveillance and electronic article surveillance (EAS) technology.
Match your inventory records
Regardless of the reason for discrepancies, you need the reconcile inventory records so they match the results of your inventory count.
If you’re using an Excel spreadsheet to manage inventory, you’ll need to manually update inventory levels for each item. If you use SimbaPOS point of sale, you can simply reconcile your inventory records in the system’s back end.
Inventory reconciliation tips
Inventory reciliation can feel tedious or prohibitively time-consuming but it’s essential for maintaining accurate inventory levels and ordering the right products at the right moment to meet demand.
Here are a few things you can do to streamline inventory reconciliation:
Stay organized
It may seem rather basic, but keeping your store and stockroom clean and organized is critical. When it’s easier for staff to locate and count merchandise, cycle counts become quicker to perform and more accurate.
A few tips we recommend include categorizing your store layout, clearly labeling stockroom shelves and assuring items are stored in the proper place or department.
Use the right tech
Human error is one of the primary causes of stock discrepancies, but when equipped with the right tech, merchants can improve the speed and accuracy of their inventory counts.
With SimbaPOS, for instance, business can add, sell, count and reconcile inventory from the same platform. With it, business owners can manage their physical retail space’s inventory from the same platform; stock levels are automatically adjusted as soon as a cashier scans a product tag at checkout.
Count inventory often
To maintain inventory accuracy and minimize the number of discrepancies you need to reconcile, it’s important to count your inventory often.
Rather than routinely performing full inventory counts (counting the inventory levels for each and product you carry), consider doing cycle counts (counting one specific product or categories inventory levels) more frequently.
Since full inventory counts are prohibitively time-consuming, most merchants only do them once or twice a year. But with cycle counts, you’re counting a lot less inventory at a time, so counting more often becomes feasible.
By cycle counting inventory regularly, merchants can keep a continuous pulse on stock levels and find the root cause of shrinkage and discrepancies, whether it’s theft, miscounting or something else, while it’s still possible to do so.
Cross-reference reconciliations
After you’ve done a few counts, it’s useful to examine those reports side by side and try to spot patterns.
For instance, is there one product or category where shrinkage consistently occurs? That could be a clue that shoplifters covet that item and are stealing it regularly. The only way to know for sure is by reviewing security footage, but at least you know where to dig deeper.
By reviewing reconciliation results next to one another, merchants can uncover patterns and find solutions to minimize shrinkage.
Keep a pulse on your inventory
Performing timely and accurate inventory counts are essential for proactively addressing the cause of shrinkage and discrepancies in your retail store. By checking inventory with regularity, merchants can optimize loss prevention while assuring that they have enough stock to meet consumer demand.